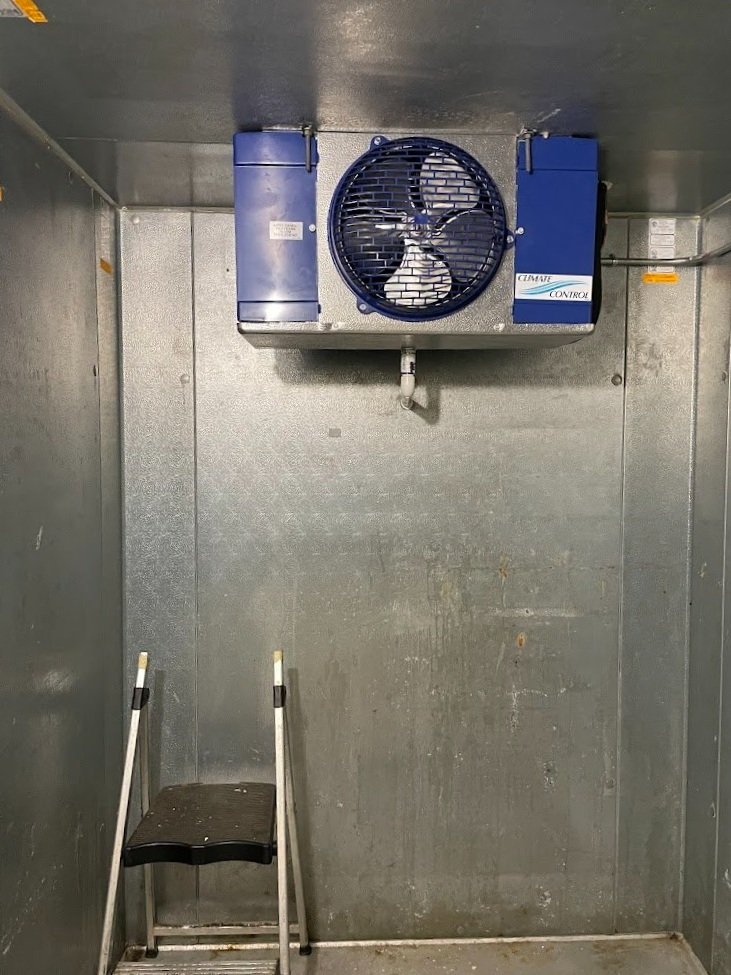
Walk-In Cooler Repair in San Antonio, TX
-
Expertise and Experience
-
Timely and Reliable Service
-
Customer-Centric Approach
-
Comprehensive Warranty and Support
Walk-in cooler repair in San Antonio, TX, provides essential service for businesses relying on commercial refrigeration to maintain freshness. A malfunctioning unit can lead to temperature fluctuations, food spoilage, and operational disruptions. Whether dealing with compressor issues, refrigerant leaks, or poor airflow, professional technicians diagnose and repair cooling systems quickly. Restoring proper function helps businesses maintain food safety standards and prevent inventory loss.
-
Common problems with walk-in coolers include inconsistent temperatures, excessive frost buildup, and unusual noises from the unit. A thorough inspection identifies the source of the issue, allowing for targeted repairs that restore efficiency. Electrical failures, worn-out door seals, and damaged components can impact performance, leading to energy waste and higher operational costs. Addressing these concerns promptly helps extend the system's lifespan while maintaining optimal cooling conditions.
Walk-in cooler repair services in San Antonio, TX, focus on delivering reliable solutions to keep refrigeration systems operating efficiently. Technicians work with various models and brands, providing expert repairs that minimize downtime. A properly functioning walk-in cooler supports food safety, reduces waste, and contributes to smooth business operations. Professional service helps restaurants, grocery stores, and other establishments maintain uninterrupted refrigeration, protecting valuable inventory and preserving product quality.
Our Reviews
Hear From Our Clients
Signs Walk-In Cooler Repair is Needed
-
Fluctuating temperatures in walk-in coolers indicate potential system problems requiring professional attention. These variations often stem from failing components, refrigerant issues, or control system malfunctions. Our technical team evaluates temperature patterns to identify underlying causes. Professional diagnosis considers factors like compressor function, thermostat operation, and seal integrity. Swift response to temperature irregularities protects stored products while preventing system damage.
-
Abnormal ice accumulation signals problems with defrost cycles or air circulation systems. This condition may indicate seal failures, damaged door components, or malfunctioning defrost mechanisms. Our experienced technicians locate and address sources of moisture infiltration and airflow restrictions. Professional evaluation determines whether ice formation stems from mechanical issues or operational factors. Proper resolution prevents damage to cooling components while maintaining optimal performance.
-
Unusual sounds from walk-in coolers often indicate mechanical problems requiring immediate attention. Rattling, humming, or grinding noises might signal compressor issues, fan problems, or loose components. Our skilled technicians identify and correct the source of concerning sounds. The professional assessment determines whether noises represent regular operation or developing issues. Early intervention when unusual sounds begin prevents more extensive system damage.
-
Rising operational costs often indicate decreased system efficiency or developing mechanical problems. Higher energy consumption might stem from failing components, refrigerant leaks, or control system issues. Our diagnostic process identifies factors contributing to excessive energy use. Professional maintenance and repairs restore optimal system performance while reducing operational expenses. Regular monitoring of system efficiency helps identify potential problems before they escalate.
Importance of Timely Walk-In Cooler Repair

Our Service Areas
Elmendorf, San Antonio, San Marcos, Floresville, Pleasanton, Converse, and Surrounding Areas
Our Walk-In Cooler Repair Services
-
Diagnostic Services
Professional evaluation begins with comprehensive system testing to accurately identify performance issues. Our technicians use advanced diagnostic tools to assess component function and system operation. This thorough approach reveals both obvious and hidden problems affecting cooling performance. Professional analysis considers all system elements while seeking problem sources. Complete diagnosis supports effective repair planning and implementation.
-
Compressor and Refrigerant Repairs
Professional compressor service maintains the heart of walk-in cooling systems. Our technicians handle refrigerant management according to current regulations and industry standards. Technical expertise supports the proper diagnosis of compressor issues and refrigerant problems. Professional service includes leak detection, refrigerant recovery, and system recharging. Quality repairs restore proper compressor function and cooling performance.
-
Thermostat and Control Panel Repairs
Professional control system repairs restore precise temperature management capabilities. Our technicians calibrate thermostats and repair control panels to maintain accurate system operation. Technical knowledge supports the proper programming of digital control systems. Professional service includes verification of adequate temperature control and monitoring functions. Reliable controls support consistent cooling performance.
-
Seal and Door Fixes
Professional door and seal repairs prevent energy waste and moisture problems. Our technicians replace damaged seals and adjust door components to maintain proper closure. Technical expertise guides the appropriate installation of replacement parts and materials. Professional service includes adjustment of door hardware and testing of seal integrity. Complete repairs prevent air infiltration and condensation issues.
-
Fan and Evaporator Repairs
Professional attention is paid to air handling components to maintain proper cooling distribution. Our technicians fix or replace malfunctioning fans and clean evaporator coils to restore an appropriate airflow. Technical knowledge supports accurate diagnosis of air circulation problems. Professional service includes testing all air handling components and verifying proper operation. Reliable air circulation maintains consistent cooling throughout the space.
Industries We Serve
-
Food service establishments face unique refrigeration challenges with high-frequency door access and variable inventory loads. Our technicians understand the critical nature of reliable cooling in commercial kitchens, where even brief system interruptions can impact food safety and service capabilities. We schedule repairs with sensitivity to peak business hours, minimizing disruption to dining operations. Restaurant-specific solutions address the demanding conditions of kitchen environments, including elevated ambient temperatures near cooking equipment and grease-laden air that affects condenser performance. Our maintenance programs align with health department inspection schedules, helping establishments maintain proper temperature documentation for regulatory compliance in this highly scrutinized industry
-
Modern grocery operations rely extensively on refrigeration systems functioning continuously across multiple temperature zones. Our specialized experience with open display cases, glass door reach-ins, and large walk-in coolers provides comprehensive support for all critical cooling infrastructure. The repair approach accounts for the substantial inventory values at risk, prioritizing temporary cooling solutions during extended repairs when necessary. Grocery-specific refrigeration includes specialized produce misting systems, refrigerated island displays, and complex defrost scheduling that requires advanced technical knowledge. Our service scheduling accommodates 24-hour operations common in this sector, with overnight repair options that maintain shopping experiences during business hours
-
Hospitality venues present diverse refrigeration requirements across food service, banquet operations, and guest amenity areas. Our repair specialists understand the premium on silent operation in guest-adjacent equipment while maintaining the heavy-duty cooling capacity needed for large-scale food preparation. The service approach incorporates discreet technician presence, respecting the refined atmosphere these establishments cultivate. Temperature stability receives particular attention in wine storage applications where fluctuations can damage valuable inventories. Our maintenance programs coordinate with event schedules, preventing system issues during critical revenue-generating functions while addressing hospitality-specific concerns like condensation management in humid public spaces
-
Healthcare refrigeration demands uncompromising reliability for storing temperature-sensitive medications, specimens, and biological materials. Our technicians receive specialized training on medical-grade cooling systems with precise temperature control requirements and comprehensive alarm monitoring. The repair procedures follow strict protocols for maintaining critical temperature ranges throughout service visits, including temporary storage solutions when necessary. Documentation processes meet regulatory standards for equipment servicing medical environments, with detailed temperature verification before returning units to service. The comprehensive maintenance programs include backup system testing and emergency response protocols tailored to healthcare facilities operating continuously with irreplaceable inventories.
-
Floral businesses require specialized cooling environments that balance temperature and humidity to maximize bloom longevity. Our refrigeration experts understand the difference between standard commercial cooling and the delicate conditions for optimal flower preservation. The repair approach includes attention to air movement patterns that prevent ethylene buildup without causing excessive evaporation. Display case lighting receives special consideration due to its heat contribution and spectral qualities affecting product appearance. Our scheduled maintenance programs coincide with slower business periods, while repair procedures maintain stable conditions that prevent costly inventory losses during system servicing, particularly important during high-volume holiday periods critical to floral business profitability.
-
The compact yet diverse refrigeration infrastructure in convenience operations includes reach-in beverage coolers, food display cases, and frozen product storage. Our technicians address the unique challenges of equipment near doorways with frequent opening patterns and resulting humidity infiltration. Repair scheduling accommodates 24-hour operations common in this industry, with minimal disruption to customer access during service visits. The maintenance approach includes special attention to condensate management systems often challenged by high-traffic environments. Our comprehensive solutions address convenience-specific concerns like beverage cooler door seal deterioration from frequent customer access and refrigerant pressure fluctuations common in systems exposed to varying ambient conditions
-
Industrial food production environments utilize sophisticated refrigeration systems operating under demanding conditions with critical temperature requirements for product safety and quality. Our specialized technical knowledge extends to large-scale ammonia systems, blast chillers, and processing-line cooling equipment requiring precise temperature control. The repair methodology incorporates food safety protocols in production environments, maintaining clean room standards where applicable. Our industrial refrigeration specialists understand the substantial production losses of cooling interruptions and implement temporary solutions during necessary system downtime. The maintenance programs synchronize with production schedules, performing comprehensive system servicing during planned facility downtime to maximize operational continuity

Financing Available!
Need help paying? Not a problem! We offer multiple financing options for repairs and installations.
Our Walk-In Cooler Repair Process
Choose A-Ok Services LLC for Walk-In Cooler Repair in San Antonio, TX
-
Every refrigeration specialist on our team holds comprehensive industry certifications, including EPA Section 608 for proper refrigerant handling and management. Our company maintains full liability insurance coverage with policy limits exceeding industry standards, providing complete protection throughout the repair process. Each technician undergoes extensive background verification and regular drug screening, establishing a workforce worthy of trust in sensitive commercial environments. The ongoing technical training program keeps our specialists current with evolving refrigeration technologies, energy efficiency standards, and safety protocols. This professional development investment translates directly into superior diagnostic capabilities, faster problem resolution, and repairs that maintain manufacturer warranty compliance across all major equipment brands.
-
Our deep understanding of San Antonio's unique climate challenges informs every repair approach, accounting for extreme summer temperatures that stress refrigeration systems beyond typical design parameters. Being headquartered locally allows our technicians to maintain extensive parts inventories specifically matched to equipment commonly installed throughout Bexar County. This regional specialization means faster repairs without waiting for distant supply chains. Our technicians possess intimate knowledge of local building codes affecting commercial refrigeration equipment, preventing compliance issues during repair procedures. The company's long-standing relationships with area suppliers create priority access to specialty components when needed for unusual systems. Climate awareness, parts availability, and regulatory knowledge form a distinct advantage over national chains lacking specific regional expertise.
-
Our strategic service center location allows technicians to reach most San Antonio businesses within 45 minutes during standard traffic conditions. The dispatch system utilizes advanced GPS tracking to route the nearest qualified technician directly to emergencies, minimizing critical downtime. For after-hours emergencies, our on-call rotation maintains multiple technicians ready to respond throughout the night, on weekends, and on holidays when walk-in cooler failures create maximum risk. The service vehicles carry comprehensive parts inventories specifically curated for common emergency repairs, eliminating delays in waiting for basic components. This rapid deployment system includes direct communication between dispatchers and clients, providing continual updates on technician arrival timing during urgent situations when every minute affects product safety and business operations.
-
Before beginning repair work, our technicians provide written estimates clearly outlining all required parts, labor components, and associated costs without hidden fees or surprising additions. The pricing structure maintains consistency regardless of business type or location, with published emergency service rates applied uniformly during after-hours calls. Multiple repair options with varying cost implications are presented whenever possible, respecting budget constraints while offering appropriate solutions for equipment age and condition. All estimates include projected completion timeframes and warranty information applicable to parts and labor. This comprehensive disclosure creates complete clarity regarding the financial investment required to resolve refrigeration issues, eliminating the uncertainty common with less forthright service providers who reveal true costs only after work completion.
A-Ok Services stands as San Antonio's premier resource for walk-in cooler repairs, bringing decades of commercial refrigeration expertise to businesses across the region.
Our certified Technicians respond quickly to service calls throughout the Greater San Antonio area, providing professional solutions that keep commercial cooling systems running efficiently. When businesses need reliable walk-in cooler repairs in San Antonio and surrounding communities, A-Ok Services delivers industry-leading technical support and repair services. Contact A-Ok Services to discuss walk-in cooler repair needs with our experienced commercial refrigeration team.
FAQ’s
-
We service and repair all walk-in coolers, including commercial, industrial, and restaurant-grade models. A-Ok Services LLC can handle it, whether a custom unit or a standard model.
-
Yes! We provide 24/7 emergency repair services for walk-in coolers to minimize downtime and prevent product loss for your business.
-
Common signs include rising temperatures, strange noises, frequent cycling, ice buildup, water leaks, or spoiled inventory.
-
We strive for same-day service. Our licensed technicians can often arrive within a few hours, especially for emergency calls in San Antonio.
-
Our technicians are trained to work on all major brands, including Kolpak, Norlake, Bally, Turbo Air, and more.
-
Possible causes include thermostat failure, refrigerant leaks, compressor issues, or dirty condenser coils. Our team will diagnose and fix the issue promptly.
-
Costs vary depending on the issue and the parts needed. After diagnosing the problem, we provide upfront, honest quotes—no hidden fees.
-
Absolutely! Regular maintenance can prevent costly repairs and extend the life of your cooler. Ask us about our customizable service plans.
-
Yes. Leaks often result from clogged drain lines, insulation issues, or door gasket problems. We’ll pinpoint the source and fix it quickly.
-
Yes, if we have the parts on hand. We carry a wide selection of replacement parts and can source specialty components quickly if needed.
-
We specialize in servicing walk-in coolers for restaurants, grocery stores, convenience stores, and other commercial facilities in San Antonio.
-
Yes, A-Ok Services LLC is fully licensed and insured for all commercial refrigeration work in San Antonio, TX.
-
Routine maintenance, regular coil cleaning, checking door seals, and monitoring temperatures can help keep your cooler running smoothly.
-
Yes! We offer energy-saving upgrades such as high-efficiency motors, LED lighting, and improved insulation systems.